Depackaging equipment is an integral part of the food industry. It enables businesses to recover and recycle materials from different types of packaging, thereby reducing waste and promoting sustainability. The process also allows for the recovery of organic material, which can be used in animal feed or composting operations.
One of the most significant advantages of using depackaging equipment in the food industry is its efficiency in separating organic materials from their packaging. This automated process ensures that valuable resources are not wasted and can be reused or recycled in various ways. For instance, food waste contained within plastic packaging can be efficiently separated: the plastic can be recycled, and the food waste can be used for composting or anaerobic digestion.
Guide to Food Industry Depackaging Equipment in 2024: Technologies, Benefits, and ROI
The food industry’s demand for efficient depackaging equipment has never been higher. Would you believe that up to 40% of food waste arrives at processing facilities still in its packaging? That’s a staggering challenge that modern depackaging equipment is solving with remarkable efficiency! I’ve spent years working with food processing facilities, and I’m amazed by how far depackaging technology has come. Let’s explore how these innovative solutions are revolutionizing waste management in 2024!
Understanding Modern Depackaging Systems
Modern depackaging equipment represents a quantum leap forward in waste processing technology. These sophisticated systems can handle everything from plastic containers to cardboard boxes, achieving separation rates that seemed impossible just a few years ago.
Core Operating Principles
- Mechanical separation through specialized paddles or grinders
- Centrifugal force for material segregation
- Hydraulic pressure systems for efficient separation
- Automated feeding and discharge mechanisms
- Integrated cleaning and sanitization systems
Material Handling Capabilities
Today’s depackaging equipment can process:
- Glass containers and bottles
- Plastic packaging (PET, HDPE, LDPE)
- Metal containers and cans
- Paper and cardboard packaging
- Multi-layer packaging materials
Leading Depackaging Technologies in 2024
The market offers several distinct approaches to depackaging, each with unique advantages:
Horizontal Paddle Systems
- Gentle separation process
- Lower microplastic generation
- Ideal for delicate packaging
- High organic material recovery rates
- Reduced maintenance requirements
Vertical Grinding Technologies
- Maximum throughput capacity
- Excellent for tough packaging
- Comprehensive material breakdown
- Enhanced separation efficiency
- Robust construction for continuous operation
Wet Separation Systems
- Superior cleaning of organic material
- Reduced cross-contamination
- Higher purity in separated streams
- Effective handling of liquid products
- Improved odor control
Key Features and Specifications
When evaluating depackaging equipment, consider these crucial specifications:
Processing Capacity
- Small systems: 2-5 tons per hour
- Medium systems: 5-15 tons per hour
- Large systems: 15+ tons per hour
- Continuous operation capability
- Adjustable throughput rates
Energy Efficiency
- Power consumption: 30-200 kW
- Variable speed drives
- Energy recovery systems
- Automated power management
- Standby mode capabilities
Quality Control and Safety Features
Modern depackaging equipment incorporates advanced safety and quality control measures:
Automated Monitoring
- Real-time performance tracking
- Foreign object detection
- Metal detection systems
- Temperature monitoring
- Pressure sensors
Safety Systems
- Emergency shutdown protocols
- Operator safety interlocks
- Explosion protection
- Noise reduction features
- Remote monitoring capabilities
Environmental Impact and Sustainability
Sustainability is a key consideration in modern depackaging equipment:
Environmental Benefits
- Reduced landfill waste
- Lower carbon footprint
- Minimized water consumption
- Improved material recovery
- Enhanced recycling rates
Material Recovery Rates
- Organic material: >99% recovery
- Packaging materials: >95% recovery
- Water content reduction: 70-90%
- Contamination reduction: >98%
- Microplastic generation: <100 particles/kg
Cost Analysis and ROI
Investment in depackaging equipment requires careful financial consideration:
Initial Investment
- Small systems: $200,000-500,000
- Medium systems: $500,000-1,000,000
- Large systems: $1,000,000+
- Installation costs: 15-25% of equipment cost
- Training and setup: 5-10% of equipment cost
Operating Costs
- Energy consumption: $5-15 per ton
- Maintenance: 3-7% of equipment cost annually
- Labor: 1-2 operators per shift
- Consumables: $1-3 per ton
- Spare parts: 2-4% of equipment cost annually
ROI Calculations
- Typical payback period: 2-4 years
- Material recovery value: $50-150 per ton
- Labor cost savings: 40-60%
- Waste disposal savings: 30-50%
- Increased processing efficiency: 20-40%
Conclusion
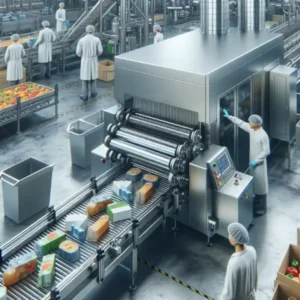
Depackaging equipment has become an indispensable tool in modern food waste management. With recovery rates exceeding 99% and ROI periods as short as two years, these systems offer compelling benefits for facilities of all sizes. Whether you’re handling expired goods, production waste, or post-consumer materials, today’s depackaging solutions provide unprecedented performance and value.
Ready to transform your facility’s waste management capabilities? Consider these key factors:
- Your specific material handling requirements
- Desired throughput capacity
- Available space and utilities
- Environmental goals
- Budget constraints
The right depackaging equipment can revolutionize your operation’s efficiency while contributing to sustainability goals. Take the next step in modernizing your facility by evaluating which system best matches your unique needs.
Investing in depackaging equipment offers numerous benefits for businesses in the food industry beyond just reducing waste disposal costs. By recovering organic material that would otherwise go to landfill, companies can create new revenue streams through selling it for use in animal feed production or energy generation via anaerobic digestion. Additionally, the process helps to conserve resources, reduce environmental impact, and meet increasing consumer demand for sustainable practices.
In conclusion, depackaging equipment plays a crucial role in the food industry. It not only helps businesses to reduce waste and save costs but also supports sustainability initiatives and contributes to circular economy principles. As awareness of environmental issues continues to grow, the use of such equipment is likely to become even more widespread in the future.