Technical Review of the Flexidry Depackager: Strengths and Weaknesses in Organic Waste Depackaging and Separation
Introduction
The Flexidry Depackager, developed by Green Creative in France, is designed specifically for separating organic material from packaging waste. With a growing emphasis on sustainable waste processing, depackaging technologies like Flexidry are increasingly essential for facilities aiming to manage food waste and recover clean organics suitable for composting or anaerobic digestion. The Flexidry Depackager is known for its gentle, low-impact separation process, which minimizes contamination by keeping packaging and organic material separate without shredding or grinding. This article provides a comprehensive analysis of the Flexidry Depackager’s strengths and weaknesses, focusing on its application in organic waste processing, particularly in separating food and organic waste from various packaging types.
Overview of Flexidry Depackager
The Flexidry Depackager operates as a non-shredding depackaging machine that gently separates organic material from its packaging. Unlike shredding systems, which tear and grind waste, Flexidry uses a slower, mechanical process designed to separate the organic fraction while leaving the packaging largely intact. This approach minimizes contamination by microplastics or smaller packaging particles, making it ideal for waste facilities prioritizing clean, high-quality organic output.
Key specifications include:
- Non-destructive separation method: Packaging remains largely whole, reducing the risk of microplastic contamination.
- Throughput capacity: Flexidry machines are designed for various operational scales, allowing for processing rates suitable for small to medium-sized waste facilities.
- Organic recovery: High organic recovery rates are reported, with processed material suitable for applications like composting or anaerobic digestion, where purity is essential for biosecurity and operational efficiency.
Technical Specifications
1. Gentle Separation without Shredding
The Flexidry Depackager uses a unique non-shredding separation technique that prioritizes maintaining the integrity of the packaging. Instead of tearing or breaking down the packaging, Flexidry employs a mechanical process that isolates the organic fraction without crushing or grinding, which is especially advantageous in applications where clean organic recovery is necessary, such as composting or anaerobic digestion.
2. Adaptability to Various Organic Waste Types
Flexidry is versatile in handling food waste, expired products, and mixed organic waste containing plastic, metal, or other packaging. This adaptability makes it useful across a range of industries, from supermarkets and food processors to waste management facilities handling post-consumer waste.
3. High-Quality Organic Output
The machine’s non-shredding design ensures that packaging contamination in the organic output is minimal, achieving high purity levels that are required for processes like biogas production. The lack of microplastic generation is an important environmental benefit, aligning with sustainability objectives.
Strengths of the Flexidry Depackager
1. Minimizes Microplastic Contamination
One of the Flexidry’s key strengths is its reduction in microplastic risk. By avoiding shredding, the machine prevents the fragmentation of plastic and other packaging materials into microplastics. This makes Flexidry particularly attractive for facilities that handle a mix of packaging materials and want to prevent microplastic pollution, especially important in regions with strict environmental regulations on microplastic emissions.
2. High Recovery Rate of Clean Organics
Flexidry’s gentle separation allows it to achieve a high recovery rate of clean, uncontaminated organic material. The organic fraction produced has been found suitable for composting and anaerobic digestion due to its purity, which avoids the typical contamination seen in shredding or grinding methods. This purity results in fewer complications during processing, such as in anaerobic digesters where contamination can impede gas production.
3. Operational Efficiency and Reduced Maintenance
Flexidry’s non-destructive separation process results in lower wear on machine parts. By minimizing direct mechanical impact, the machine incurs less frequent maintenance, reducing operational costs. Additionally, operators benefit from the machine’s low-maintenance requirements, as the process avoids the wear and tear associated with high-impact grinding or shredding components.
4. Suitable for Various Industries and Waste Types
Flexidry has found applications across a wide spectrum of industries, including:
- Food retail: For separating expired or unsold food items from packaging, ensuring clean organic waste for reuse or composting.
- Food processing: For managing production waste with different packaging types.
- Municipal waste facilities: Where high levels of organic waste must be separated from diverse packaging.
This versatility enables Flexidry to integrate effectively within various waste processing systems.
Weaknesses of the Flexidry Depackager
1. Lower Throughput Capacity Compared to Shredding Systems
While Flexidry excels at producing clean, uncontaminated organics, its throughput capacity can be lower than that of high-speed shredding or grinding systems, which are designed for high-volume processing. Facilities with extremely high waste volumes may find Flexidry’s output rates insufficient for their needs, particularly if they are prioritizing rapid processing over purity.
2. Less Effective with Very Rigid Packaging
Although Flexidry is versatile, it may struggle with extremely rigid or thick packaging materials, which can be more challenging to separate without tearing or breaking. In cases where waste streams contain substantial quantities of metal cans or glass, the Flexidry may require pre-sorting or specialized handling to avoid complications.
3. Higher Initial Investment Costs
The specialized design of the Flexidry Depackager, focused on maintaining purity in organic output, can involve a higher upfront cost compared to conventional shredders. While this cost may be offset by savings on maintenance and regulatory compliance, smaller facilities with limited budgets might find the initial investment challenging without external funding or incentives.
4. Limited Integration with Some Waste Processing Systems
The Flexidry Depackager is highly specialized for organic waste separation and may not be easily integrated into systems that require multi-functional equipment or that process high proportions of non-organic waste. Waste facilities that handle significant amounts of mixed or non-organic waste may need additional machinery to complement the Flexidry’s focus on organic separation.
Case Studies and Real-World Applications
1. Supermarket Chain in France
A French supermarket chain implemented the Flexidry Depackager to handle expired food items, separating organic waste from packaging before sending it to a biogas production facility. The chain reported that the Flexidry’s gentle process achieved a high recovery rate of uncontaminated organics, which helped maximize biogas yield at the digestion facility. Additionally, because the packaging was not shredded, there were fewer issues with microplastic contamination in the digestate, an important factor in meeting environmental standards.
2. Food Waste Processing in the United Kingdom
A food waste processing plant in the UK used Flexidry to separate post-consumer organic waste from packaging collected from restaurants and cafeterias. Operators observed a significant reduction in contamination levels in the organic fraction compared to previous shredding-based methods, which reduced operational complications in downstream composting. The plant was able to produce compost that met regulatory standards without requiring extensive additional treatment, highlighting the Flexidry’s suitability for applications where purity is essential.
3. Municipal Waste Facility in Germany
A municipal waste facility in Germany adopted Flexidry for processing organic-rich domestic waste streams. The machine’s ability to separate organics without breaking down plastic packaging allowed the facility to produce cleaner compost and improved the quality of output in line with European environmental regulations. However, operators noted the need for occasional pre-sorting, as the Flexidry had difficulty with particularly rigid or multi-layered packaging materials.
Comparison with Alternative Depackaging Technologies
When compared to shredding-based depackaging technologies, the Flexidry’s strengths in organic purity and microplastic reduction stand out. Traditional shredders often produce fragmented plastic particles that contaminate organic material, creating challenges for composting and biogas applications. However, shredding systems offer higher throughput and are more effective with mixed waste containing rigid packaging.
For facilities prioritizing clean organic output over processing speed, the Flexidry Depackager presents a preferable solution, especially in compliance-driven markets with strict contamination limits. In contrast, large facilities with diverse waste streams may benefit from systems that incorporate both shredding and non-destructive separation methods to handle a wider range of waste materials efficiently.
Conclusion
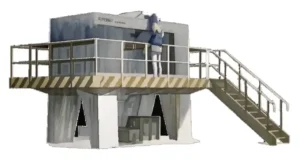
The Flexidry Depackager offers a specialized, environmentally conscious solution for waste facilities focused on organic waste separation and purity. Its non-shredding, low-impact separation technique minimizes microplastic contamination, making it highly suitable for applications in composting and anaerobic digestion. With strengths in organic purity, reduced maintenance, and suitability for various types of organic waste, the Flexidry Depackager is an excellent choice for facilities focused on sustainability and high-quality output.
However, the Flexidry may face limitations with rigid packaging materials and for facilities with high throughput requirements. Its higher initial cost may also be a factor for smaller facilities, though the long-term benefits of reduced maintenance and regulatory compliance may outweigh these costs.
In summary, Flexidry provides an innovative solution that meets the growing demand for environmentally friendly waste processing technologies. As regulatory pressures and sustainability goals continue to shape the industry, Flexidry stands out as a reliable, efficient option for those seeking cleaner organic waste processing.
Developer of innovative waste processing solutions
Industry Sector: Waste Processing
Business Location: France
Address:
Flexidry
9 bis avenue du Bouton d’Or
Z.A Les Petits Carreaux
94370 Sucy-en-Brie / FRANCE
Phone: +33 (0)1 43 77 85 42
Website:
Green Creative: https://www.green-creative.com/
Opening Hours:
8am to 5pm Weekdays