Maintaining food depackaging equipment is a critical aspect of ensuring the smooth operation, safety, and longevity of your food processing line. Proper maintenance not only minimizes downtime and extends the lifespan of your machinery but also ensures that your products meet the highest standards of quality and hygiene. In this comprehensive guide, we delve into essential tips and best practices for maintaining your food depackaging equipment effectively.
Importance of Regular Maintenance
Regular maintenance of depackaging equipment is paramount for several reasons:
- Operational Efficiency: Well-maintained equipment operates more efficiently, reducing energy consumption and maximizing output.
- Product Quality: Consistent performance ensures that packaging meets quality standards, preventing product spoilage and contamination.
- Safety: Maintenance helps identify and mitigate potential hazards, safeguarding workers and consumers alike.
- Cost Savings: Preventative maintenance reduces the likelihood of major repairs and costly downtime.
- Compliance: Adhering to maintenance schedules ensures compliance with industry regulations and standards.
Key Maintenance Tips for Depackaging Equipment
1. Develop a Comprehensive Maintenance Schedule
Creating a detailed maintenance schedule is the foundation of effective equipment upkeep. Consider the following steps:
- Inventory Assessment: List all depackaging equipment and their respective maintenance needs.
- Frequency Determination: Establish how often each piece of equipment requires maintenance, based on manufacturer recommendations and usage levels.
- Task Allocation: Assign specific maintenance tasks, such as cleaning, lubrication, and parts inspection, to designated times.
- Documentation: Keep accurate records of all maintenance activities to track performance and identify recurring issues.
Video Suggestion: Tutorial on creating a maintenance schedule using software tools.
2. Clean Equipment Regularly
Cleanliness is crucial in food processing environments to prevent contamination and ensure equipment longevity.
- Daily Cleaning: Wipe down surfaces, remove debris, and sanitize equipment after each shift.
- Deep Cleaning: Conduct thorough cleanings at regular intervals, focusing on hard-to-reach areas and components.
- Use Appropriate Cleaners: Employ food-grade cleaning agents that effectively remove residues without damaging equipment.
Image Suggestion: Technician performing a deep clean on depackaging machinery.
3. Inspect and Replace Worn Parts
Regular inspections help identify wear and tear before it leads to equipment failure.
- Visual Inspections: Check for signs of damage, such as cracks, fraying, or corrosion.
- Functional Tests: Assess the performance of moving parts to ensure they operate smoothly.
- Timely Replacement: Replace worn or faulty components promptly to avoid breakdowns and maintain optimal performance.
Bullet Point List: Common parts that require regular inspection and replacement, such as belts, gears, and seals.
4. Lubricate Moving Parts
Proper lubrication reduces friction and wear, enhancing the efficiency and lifespan of your equipment.
- Select the Right Lubricants: Use lubricants recommended by the manufacturer to ensure compatibility with equipment materials.
- Regular Application: Follow a consistent lubrication schedule to maintain smooth operation.
- Avoid Over-Lubrication: Excess lubricant can attract dirt and cause buildup, leading to potential issues.
5. Monitor Equipment Performance
Keeping a close eye on how your equipment performs can help detect issues early.
- Performance Metrics: Track key indicators such as processing speed, accuracy, and error rates.
- Data Analysis: Use data analytics to identify trends and predict potential failures.
- Responsive Action: Address deviations from normal performance promptly to prevent minor issues from escalating.
Best Practices for Depackaging Equipment Maintenance
Implement Preventative Maintenance Programs
Preventative maintenance (PM) focuses on regular, scheduled maintenance tasks designed to prevent unexpected equipment failures.
- Advantages of PM:
– Reduces unplanned downtime – Extends equipment life – Enhances safety and compliance
- PM Strategies:
– Routine inspections and servicing – Predictive maintenance using advanced monitoring tools – Training staff on PM procedures
Train and Empower Your Maintenance Team
A knowledgeable and skilled maintenance team is essential for effective equipment upkeep.
- Comprehensive Training: Ensure that technicians are well-versed in the operation and maintenance of depackaging equipment.
- Ongoing Education: Provide continuous learning opportunities to keep the team updated on the latest technologies and maintenance techniques.
- Empowerment: Encourage team members to take initiative in identifying and solving maintenance issues.
Utilize Quality Replacement Parts
Using high-quality replacement parts ensures reliability and performance.
- OEM Parts: Opt for Original Equipment Manufacturer (OEM) parts to guarantee compatibility and longevity.
- Inventory Management: Maintain an inventory of critical spare parts to facilitate quick replacements and minimize downtime.
- Supplier Relationships: Build strong relationships with reputable suppliers to ensure the timely availability of parts.
Incorporate Technology and Automation
Leveraging technology can enhance maintenance efficiency and accuracy.
- Computerized Maintenance Management Systems (CMMS): Implement CMMS to streamline maintenance scheduling, tracking, and documentation.
- Predictive Analytics: Use sensors and data analytics to predict equipment failures before they occur.
- Automation Tools: Integrate automated systems for routine maintenance tasks, reducing manual effort and human error.
Image Suggestion: Dashboard of a CMMS showing scheduled maintenance tasks.
Troubleshooting Common Depackaging Equipment Issues
Despite regular maintenance, issues may still arise. Here are common problems and their solutions:
1. Equipment Not Starting
- Check Power Supply: Ensure that the equipment is properly connected to a power source and that the outlet is functioning.
- Inspect Electrical Components: Look for damaged wires, blown fuses, or faulty switches and replace as necessary.
- Reset Systems: Some machines have reset buttons or circuit breakers that may need to be activated after a power outage.
2. Inconsistent Performance
- Calibration: Recalibrate the equipment to ensure accurate operation.
- Sensor Cleaning: Dirty or malfunctioning sensors can lead to inconsistent performance; clean or replace them as needed.
- Software Updates: Ensure that the equipment’s software is up to date to prevent operational glitches.
3. Jamming or Sticking
- Clear Obstructions: Remove any foreign objects or debris that may be causing jams.
- Adjust Tolerances: Fine-tune the equipment settings to prevent materials from getting stuck.
- Inspect Moving Parts: Check for misalignments or damaged components that could be contributing to the issue.
4. Excessive Noise or Vibration
- Tighten Components: Loose parts can cause vibrations and noise; ensure all components are securely fastened.
- Balance Rotating Parts: Unbalanced rotors or belts can lead to excessive vibration; balance or replace them as necessary.
- Lubricate Moving Parts: Proper lubrication can minimize noise and reduce wear on moving components.
Scheduling Regular Maintenance Checks
Establishing a consistent maintenance routine is essential for keeping your depackaging equipment in optimal condition.
Daily Checks
- Visual Inspections: Examine equipment for visible signs of wear or damage.
- Cleaning: Perform basic cleaning tasks to remove debris and prevent buildup.
- Operational Tests: Run the equipment briefly to ensure it starts and operates correctly.
Weekly Checks
- Detailed Inspections: Conduct more thorough examinations of critical components.
- Lubrication: Apply lubricants to moving parts as per the maintenance schedule.
- Performance Monitoring: Review performance metrics to identify any irregularities.
Monthly Checks
- Comprehensive Maintenance: Execute in-depth maintenance tasks, including part replacements and system calibrations.
- Safety Audits: Inspect safety features and protocols to ensure they are functioning properly.
- Documentation Review: Update maintenance records and analyze data for trends or recurring issues.
Annual Checks
- Major Overhaul: Perform extensive maintenance, such as disassembling components for thorough cleaning and inspection.
- Software Upgrades: Update or upgrade the equipment’s software to the latest version.
- Training Refreshers: Provide additional training to maintenance staff to reinforce best practices and introduce new techniques.
Bullet Point List: Maintenance tasks categorized by daily, weekly, monthly, and annual schedules.
Benefits of Professional Maintenance Services
While in-house maintenance teams are valuable, partnering with professional maintenance service providers offers distinct advantages:
- Expertise: Professional technicians bring specialized knowledge and experience, ensuring high-quality maintenance.
- Efficiency: Outsourced maintenance can often be performed more quickly, reducing downtime and disrupting operations minimally.
- Access to Advanced Tools: Professional services utilize the latest tools and technologies for accurate diagnostics and effective repairs.
- Cost-Effectiveness: Outsourcing maintenance can be more economical than maintaining a full-time in-house team, especially for smaller operations.
- Extended Equipment Lifespan: Regular professional maintenance can significantly prolong the life of your depackaging equipment, maximizing your investment.
Image Suggestion: Professional maintenance team working on depackaging equipment.
Implementing a Maintenance Management System
A Maintenance Management System (MMS) can revolutionize how you approach equipment maintenance, offering numerous benefits:
Centralized Data Repository
An MMS centralizes all maintenance-related information, making it easily accessible and organized.
- Maintenance Logs: Store detailed records of all maintenance activities, including dates, tasks performed, and parts used.
- Equipment History: Track the history and performance of each piece of equipment to inform maintenance decisions.
- Inventory Management: Monitor spare parts inventory levels to ensure availability when needed.
Enhanced Scheduling and Planning
An MMS facilitates efficient scheduling and planning of maintenance tasks.
- Automated Reminders: Receive notifications for upcoming maintenance tasks, reducing the risk of missed schedules.
- Resource Allocation: Allocate resources effectively by understanding the workload and requirements of each maintenance task.
- Task Prioritization: Prioritize maintenance activities based on equipment criticality and current operational needs.
Improved Communication and Collaboration
An MMS fosters better communication among maintenance teams and other departments.
- Task Assignments: Assign tasks to specific team members, ensuring clarity and accountability.
- Real-Time Updates: Share real-time updates on maintenance progress, allowing for better coordination.
- Reporting Tools: Generate reports to share insights and performance metrics with stakeholders.
Video Suggestion: Demonstration of a Maintenance Management System in action.
Ensuring Compliance with Regulatory Standards
Compliance with industry regulations is non-negotiable in the food processing sector. Proper maintenance plays a significant role in meeting these standards.
Understanding Relevant Regulations
Familiarize yourself with the regulations that apply to your operations, such as:
- FDA Guidelines: Follow the Food and Drug Administration’s standards for food safety and equipment sanitation.
- HACCP Standards: Implement Hazard Analysis Critical Control Points (HACCP) principles to manage food safety risks.
- Local Health Codes: Adhere to local health and safety regulations pertinent to your facility and operations.
Documentation and Record-Keeping
Maintain comprehensive records to demonstrate compliance during inspections and audits.
- Maintenance Logs: Document all maintenance activities, including tasks performed, dates, and personnel involved.
- Inspection Reports: Keep detailed reports of inspections and any corrective actions taken.
- Training Records: Maintain records of staff training and certifications related to equipment maintenance and food safety.
Regular Audits and Assessments
Conduct periodic audits to ensure ongoing compliance and identify areas for improvement.
- Internal Audits: Schedule regular internal reviews of maintenance practices and compliance status.
- Third-Party Inspections: Engage external auditors to provide unbiased assessments of your maintenance programs and compliance.
- Continuous Improvement: Use audit findings to enhance maintenance procedures and address any compliance gaps.
Leveraging Technology for Advanced Maintenance
Integrating advanced technologies can elevate your maintenance practices, offering greater precision and efficiency.
Predictive Maintenance
Predictive maintenance uses data analytics and machine learning to forecast equipment failures before they occur.
- Sensor Integration: Install sensors on critical components to monitor parameters like temperature, vibration, and pressure in real-time.
- Data Analysis: Utilize analytics platforms to interpret sensor data and identify patterns indicative of potential failures.
- Proactive Repairs: Schedule maintenance activities based on predictive insights, preventing unexpected downtime and costly repairs.
Internet of Things (IoT)
IoT technology connects your equipment to the internet, enabling seamless data collection and communication.
- Remote Monitoring: Access real-time data on equipment performance from any location.
- Automated Alerts: Receive automatic notifications for anomalies or performance deviations.
- Integration with CMMS: Sync IoT data with your Maintenance Management System for comprehensive maintenance planning.
Augmented Reality (AR) and Virtual Reality (VR)
AR and VR technologies provide innovative solutions for maintenance training and support.
- Interactive Training: Use AR/VR simulations to train maintenance staff in a safe and engaging environment.
- Remote Assistance: Employ AR tools to offer remote guidance to technicians, enhancing troubleshooting and repair processes.
- Visualization: Overlay digital information onto physical equipment to aid in complex maintenance tasks.
Image Suggestion: Illustration of IoT sensors on depackaging equipment.
Addressing Common Maintenance Challenges
Even with the best practices in place, maintenance teams may encounter various challenges. Here’s how to address some common issues:
Limited Resources
- Prioritize Tasks: Focus on critical maintenance activities that directly impact operations and safety.
- Optimize Scheduling: Align maintenance tasks with production schedules to minimize disruptions.
- Invest in Training: Enhance the efficiency of your team by providing comprehensive training and development opportunities.
Resistance to Change
- Communicate Benefits: Clearly articulate the advantages of new maintenance practices and technologies to gain buy-in from stakeholders.
- Involve the Team: Engage maintenance staff in the planning and implementation process to foster ownership and acceptance.
- Provide Support: Offer adequate support and resources to ease the transition to new maintenance systems or procedures.
Keeping Up with Technological Advancements
- Continuous Learning: Encourage ongoing education and training to keep your team updated on the latest technologies.
- Collaborate with Experts: Partner with technology providers and experts to stay informed about emerging maintenance solutions.
- Regular Reviews: Periodically assess your maintenance strategies to incorporate new advancements that can enhance efficiency and effectiveness.
Conclusion
Effective maintenance of food depackaging equipment is indispensable for achieving operational excellence, ensuring product quality, and maintaining compliance with industry standards. By implementing a comprehensive maintenance schedule, investing in training, leveraging advanced technologies, and partnering with professional maintenance services, you can safeguard your equipment against failures and optimize your production processes.
Maintaining your depackaging equipment isn’t just a routine task—it’s a strategic investment in the success and sustainability of your food processing operations. Contact us today to learn more about our specialized maintenance services and how we can help keep your equipment running smoothly and efficiently.
CTA Suggestion: “Ready to optimize your depackaging equipment maintenance? Get in touch with our experts today!“
Frequently Asked Questions (FAQs)
Why is regular maintenance of depackaging equipment important?
Regular maintenance ensures that your equipment operates efficiently, reduces the risk of unexpected downtime, maintains product quality, and extends the lifespan of your machinery. It also helps in complying with safety and industry regulations.
How often should I perform maintenance on my depackaging equipment?
The frequency of maintenance depends on the equipment usage, manufacturer recommendations, and operational environment. Typically, daily, weekly, monthly, and annual maintenance tasks should be scheduled to cover all aspects of equipment upkeep.
What are the common signs that my depackaging equipment needs maintenance?
Common signs include unusual noises, inconsistent performance, increased energy consumption, visible wear and tear, frequent jams or stoppages, and error messages on control panels.
Can I perform maintenance myself, or should I hire professionals?
While basic maintenance tasks can be handled in-house, professional maintenance services offer specialized expertise, advanced tools, and comprehensive support that ensure your equipment is maintained to the highest standards.
What technologies can enhance depackaging equipment maintenance?
Technologies such as Computerized Maintenance Management Systems (CMMS), Predictive Maintenance using IoT sensors, and Augmented Reality (AR) for training and remote assistance can significantly enhance maintenance efficiency and effectiveness.
Implementing these essential maintenance tips will ensure that your food depackaging equipment remains reliable, efficient, and compliant, ultimately contributing to the overall success of your food processing operations. Don’t wait for problems to arise—take proactive steps today to maintain your machinery and sustain your business growth.
Maintaining your food depackaging equipment is an essential practice that not only prolongs the lifespan of your equipment but also ensures efficiency and safety during operations. Regular maintenance can help prevent unexpected breakdowns, which often result in production delays and significant repair costs. Here are some essential tips to keep your food depackaging equipment in top-notch condition.
1. Regular Inspection: A routine inspection is a fundamental part of preventive maintenance. It involves checking all parts of the depackaging machine for wear and tear, including belts, motors, sensors, etc. Inspect the equipment for any signs of damage or malfunctioning regularly, and replace or repair components as necessary.
2. Cleaning: Proper cleaning is vital to maintain hygiene standards and ensure efficient operation of the machinery. Food residues left in the machine can attract pests and cause bacterial growth, leading to food contamination. Therefore, it’s critical to clean all parts thoroughly after every use with suitable cleaning agents.
3. Lubrication: Most machines require regular lubrication for smooth operation. Lack of lubrication can lead to increased wear on moving parts and eventually lead to a breakdown. Check the manufacturer’s recommendation for lubricants and lubrication intervals.
4. Adhere to Manufacturer’s Guidelines: Always follow the manufacturer’s guidelines regarding usage and maintenance procedures for your specific depackaging equipment model. These instructions provide detailed information about correct usage methods, recommended spare parts, troubleshooting techniques, etc.
5. Scheduled Servicing: Regular professional servicing can help identify issues that might not be noticeable during daily inspections. Such services typically include thorough cleaning, calibration checks, replacing worn-out parts among other tasks that enhance performance.
6. Training Staff: Ensure all staff members operating these machines have received adequate training on how to use them correctly and safely, as well as perform basic maintenance tasks like cleaning and inspecting parts for wear.
7. Keep Spare Parts Handy: Having spare parts at hand can save precious time during breakdowns. Identify the components of your depackaging machine that are prone to wear and tear, and keep a stock of these parts for quick replacements.
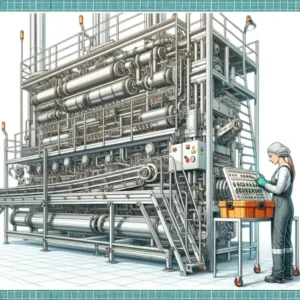
8. Record Keeping: Keep a detailed log of all maintenance activities, including servicing, part replacements, repairs, etc. This record will help you identify patterns in equipment behaviour over time, allowing for more effective preventive maintenance planning.
In conclusion, the maintenance of food depackaging equipment is not a task to be taken lightly. (See our depackaging equipment guide here.) It is crucial for extending the lifespan of your equipment, ensuring safe and efficient operations, and meeting food safety regulations. By following these tips and developing a structured routine for inspection, cleaning, lubrication, and servicing, you can prevent unexpected breakdowns and costly repairs.